Fundamentals of Heat Exchanger Design, Second Edition builds upon the widely-used First Edition, a text often considered to be the most prominent single-volume heat exchanger text on the market. The new and improved Second Edition serves as an equally comprehensive resource, updated to suit the latest technologies and design methods being used in the Heat Exchanger field. Written by First-Edition author Dusan P. Sekulic, this text addresses the latest developments in the industry, including a brand-new chapter on the manufacturing of compact heat exchangers. After opening with a basic introduction to heat exchanger types and design methods, the book goes on to cover more specialized topics such as such as the design of recuperators and regenerators, pressure drop analysis, geometric properties, flow friction, fouling and corrosion, and more. With many significant revisions throughout, this new edition offers more streamlined content while maintaining the consistent, detailed coverage of the fundamentals of the topic that readers appreciated in the First Edition. These unique features position the Second Edition of Fundamentals of Heat Exchanger Design as the ideal text for both engineering professionals and advanced students alike.
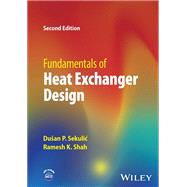
Fundamentals of Heat Exchanger Design
by Sekulic, Dusan P.; Shah, Ramesh K.-
This Item Qualifies for Free Shipping!*
*Excludes marketplace orders.
Buy New
Rent Textbook
Rent Digital
Used Textbook
We're Sorry
Sold Out
How Marketplace Works:
- This item is offered by an independent seller and not shipped from our warehouse
- Item details like edition and cover design may differ from our description; see seller's comments before ordering.
- Sellers much confirm and ship within two business days; otherwise, the order will be cancelled and refunded.
- Marketplace purchases cannot be returned to eCampus.com. Contact the seller directly for inquiries; if no response within two days, contact customer service.
- Additional shipping costs apply to Marketplace purchases. Review shipping costs at checkout.
Summary
Author Biography
Dusan P. Sekulic is a professor at the University of Kentucky College of Engineering. His work has been featured in over 200 publications, and he has authored or co-authored three previous books.
Ramesh K. Shah worked as a research professor at the Rochester Institute of Technology, as well as a senior staff research scientist at Delphi Harrison Thermal Systems and General Motors Corporation. He has authored and contributed to countless journal articles, books, conference papers, and more.
Table of Contents
Preface
Nomenclature
1 Heat Exchangers: Semantics
1.1 Heat Transfer in a Heat Exchanger
1.1.1 Heat Exchanger as a Part of a System
1.1.2 Heat Exchanger as a Component
1.2 Modelling a Heat Exchanger
1.2.1 Temperature Distributions in Counterflow and Parallel flow
1.2.2 True Meaning of the Heat Exchanger Effectiveness
1.2.3 Temperature Difference Distributions
1.2.4 Temperature Distributions in Crossflow Exchangers
1.3 Irreversibility in Heat Exchangers
1.3.1 Entropy Generation Caused by Finite Temperature Differences
1.3.2 Entropy Generation Associated with Fluid Mixing
1.3.3 Entropy Generation Caused by Fluid Friction
1.4 Thermodynamic Irreversibility and Temperature Cross Phenomena
1.4.1 Maximum Entropy Generation
1.4.2 External Temperature Cross and Fluid Mixing Analogy
1.4.3 Thermodynamic Analysis for 1-2 TEMA J Shell and Tube Exchanger
1.5 Heuristic Approach to an Assessment of Heat Exchanger Effectiveness
1.6 Energy, Exergy and Cost Balances in the Analysis of Heat Exchangers
1.6.1 Temperature-Enthalpy Rate Change Diagram
1.6.2 Analysis Based on an Energy Rate Balance
1.6.3 Analysis Based on Energy/Enthalpy and Cost Rate Balancing
1.6.4 Analysis Based on an Exergy Rate Balance
1.6.5 Thermodynamic Figure of Merit for Assessing Exchanger Performance
1.6.6 Accounting for the Cost of Exergy Losses in a Heat Exchanger
1.7 Performance Evaluation Criteria Based on the Second Law of Thermodynamics
References
2 Overview of Heat Exchanger Design Methodology: The Art
2.1 Heat Exchanger Design Methodology
2.1.1 Process and Design Specifications
2.1.2 Thermal and Hydraulic Design
2.1.3 Mechanical Design
2.1.4 Manufacturing Considerations and Cost Estimates
2.1.5 Trade-off Factors
2.1.6 Optimum Design
2.1.7 Other Considerations
2.2 Interactions Among Design Considerations
2.3 Design Heat Exchangers for Manufacturing
2.3.1 Brazed Heat Exchangers
2.3.2 Additive Manufacturing Heat Exchangers (3-D Printing)
References
3 Thermal Design Theory for Recuperators
3.1 Heat Flow and Thermal Resistance
3.2 Heat Exchanger Design Variables/Parameters
3.2.1 Assumptions for Heat Exchanger Analysis
3.2.2 Problem Formulation
3.2.3 Definitions of Dimensional Variables
3.2.4 Thermal Size and UA
3.3 The ε-NTU Method
3.3.1 Heat Exchanger Effectiveness ε
3.3.2 Heat Capacity Rate Ratio C*
3.3.3 Number of Transfer Units NTU
3.4 Effectiveness – NTU Relationships
3.4.1 Single-Pass Exchangers/Counterflow Exchangers
3.4.2 Exchangers with Other Flow Arrangements
3.4.3 Interpretation of -NTU Results
3.4.4 Stream Symmetry
3.5 The P-NTU Method
3.5.1 Temperature Effectiveness P
3.5.2 Number of Transfer Units, NTU
3.5.3 Heat Capacity Rate Ratio R
3.5.4 General P–NTU Functional Relationship
3.6 P–NTU Relationships
3.6.1 Parallel Counterflow Exchanger, Shell Fluid Mixed, 1–2
TEMA E Shell
ass Exchangers
3.7 The Mean Temperature Difference Method
3.7.1 Log-Mean Temperature Difference, LMTD
3.7.2 Log-Mean Temperature Difference Correction Factor F
3.8 F Factors for Various Flow Arrangements
3.8.1 Counterflow Exchanger
3.8.2 Parallelflow Exchanger
3.8.3 Other Basic Flow Arrangements
3.8.4 Heat Exchanger Arrays and Multipassing
3.9 Comparison of the ε-NTU, P–NTU, and MTD Methods
3.9.1 Solutions to the Sizing and Rating Problems
3.9.2 The ε-NTU Method Revisited
3.9.3 The P-NTU Method Revisited
3.9.4 The MTD Method Revisited
3.10 The and P1-P2 Methods
3.10.1 The Method
3.10.2 The P1-P2 Method
3.11 Solution Methods for Determining Exchanger Effectiveness
3.11.1 Exact Analytical Methods
3.11.2 Approximate Methods
3.11.3 Numerical Methods
3.11.4 Matrix Formalism
3.11.5 Chain Rule Methodology
3.11.6 Flow-Reversal Symmetry
3.11.7 Rules for the Determination of Exchanger Effectiveness
with One Fluid Mixed
3.12 Heat Exchanger Design Problems
References
4 Relaxation of Selected Design Assumptions. Extended SUrfaces
4.1 Longitudinal Wall Heat Conduction Effects
4.1.1 Exchangers with C* = 0
4.1.2 Single-Pass Counterflow Exchanger
4.1.3 Single-Pass Parallelflow Exchanger
4.1.4 Single-Pass Unmixed–Unmixed Crossflow Exchanger
4.1.5 Other Single-Pass Exchangers
4.1.6 Multipass Exchangers
4.2 Nonuniform Overall Heat Transfer Coefficients
4.2.1 Temperature Effect
4.2.2 Length Effect
4.2.3 Combined Effect
4.3 Additional Considerations for Extended Surface Exchangers
4.3.1 Thin Fin Analysis
4.3.2 Fin Efficiency
4.3.3 Fin Effectiveness
4.3.4 Extended Surface Efficiency
4.4 Additional Considerations for Shell-and-Tube Exchangers
4.4.1 Shell Fluid Bypassing and Leakage
4.4.2 Unequal Heat Transfer Area in Individual Exchanger Passes
4.4.3 Finite Number of Baffles
4.5 Flow Maldistribution
4.5.1 Geometry-induced Flow Maldistribution
4.5.2 Operating Condition-induced Flow Maldistribution
4.5.3 Mitigation of Flow Maldistribution
References
5 Thermal Design Theory for Regenerators
5.1 Heat Transfer Analysis
5.1.1 Assumptions for Regenerator Heat Transfer Analysis
5.1.2 Definitions and Description of Important Parameters
5.1.3 Governing Equations
5.2 The ε-NTUo Method
5.2.1 Dimensionless Groups
5.2.2 Influence of Core Rotation and Valve Switching Frequency
5.2.3 Convection Conductance Ratio (hA)*
5.2.4 ε -NTUo Results for a Counterflow Regenerator
5.2.5 ε -NTUo Results for a Parallelflow Regenerator
5.3 The Method
5.3.1 Comparison of the ε -NTUo and Methods
5.3.2 Solutions for a Counterflow Regenerator
5.3.3 Solution for a Parallelflow Regenerator
5.4 Influence of Longitudinal Wall Heat Conduction
5.5 Influence of Transverse Wall Heat Conduction
5.5.1 Simplified Theory
5.6 Influence of Pressure and Carryover Leakages
5.6.1 Modeling of Pressure and Carryover Leakages for a Rotary
Regenerator
5.7 Influence of Matrix Material, Size, and Arrangement
References
6 Heat Exchanger Pressure Drop Analysis
6.1 Introduction
6.1.1 Importance of Pressure Drop
6.1.2 Fluid Pumping Devices
6.1.3 Major Contributions to the Heat Exchanger Pressure Drop
6.1.4 Assumptions for Pressure Drop Analysis
6.2 Extended Surface Heat Exchanger Pressure Drop
6.2.1 Plate-Fin Heat Exchangers
6.2.2 Tube-Fin Heat Exchangers
6.3 Regenerator Pressure Drop
6.4 Tubular Heat Exchanger Pressure Drop
6.4.1 Tube Banks
6.4.2 Shell-and-Tube Exchangers
6.5 Plate Heat Exchanger Pressure Drop
6.6 Pressure Drop Associated with Fluid Distribution Elements
6.6.1 Pipe Losses
6.6.2 Sudden Expansion and Contraction Losses
6.6.3 Bend Losses
6.7 Pressure Drop Presentation
6.7.1 Nondimensional Presentation of Pressure Drop Data
6.7.2 Dimensional Presentation of Pressure Drop Data
6.8 Pressure Drop Dependence on Geometry and Fluid Properties
References
7 Surface Heat Transfer and Flow Friction Characteristics
7.1 Basic Concepts
7.1.1 Boundary Layers
7.1.2 Types of Flows
7.1.3 Free and Forced Convection
7.1.4 Basic Definitions
7.2 Dimensionless Groups
7.2.1 Fluid Flow
7.2.2 Heat Transfer 446
7.2.3 Dimensionless Surface Characteristics as a Function of the Reynolds Number
7.3 Experimental Techniques for Determining Surface Characteristics
7.3.1 Steady-State Kays and London Technique
7.3.2 Wilson Plot Technique
7.3.3 Transient Test Techniques
7.3.4 Friction Factor Determination
7.4 Analytical and Semiempirical Heat Transfer and Friction Factor Correlations for Simple Geometries
7.4.1 Fully Developed Flows
7.4.2 Hydrodynamically Developing Flows
7.4.3 Thermally Developing Flows
7.4.4 Simultaneously Developing Flows
7.4.5 Extended Reynolds Analogy
7.4.6 Limitations of j vs. Re Plot
7.5 Experimental Heat Transfer and Friction Factor Correlations for Complex Geometries
7.5.1 Tube Bundles
7.5.2 Plate Heat Exchanger Surfaces
7.5.3 Plate-Fin Extended Surfaces
7.5.4 Tube-Fin Extended Surfaces
7.5.5 Regenerator Surfaces
7.6 Influence of Temperature-Dependent Fluid Properties
7.6.1 Correction Schemes for Temperature-Dependent Fluid Properties
7.7 Influence of Superimposed Free Convection
7.7.1 Horizontal Circular Tubes
7.7.2 Vertical Circular Tubes
7.8 Influence of Superimposed Radiation
7.8.1 Liquids as Participating Media
7.8.2 Gases as Participating Media
References
8 Geometry of Heat Exchanger’s Surfaces
8.1 Tubular Heat Exchangers
8.1.1 Inline Arrangement
8.1.2 Staggered Arrangement
8.2 Tube-Fin Heat Exchangers
8.2.1 Circular Fins on Circular Tubes
8.2.2 Plain Flat Fins on Circular Tubes
8.2.3 General Geometric Relationships for Tube-Fin Exchangers
8.3 Plate-Fin Heat Exchangers
8.3.1 Offset Strip Fin Exchanger
8.3.2 Corrugated Louver Fin Exchanger
8.3.3 General Geometric Relationships for Plate-Fin Surfaces
8.4 Regenerators with Continuous Cylindrical Passages
8.4.1 Triangular Passage Regenerator
8.5 Shell-and-Tube Exchangers with Segmental Baffles
8.5.1 Tube Count
8.5.2 Window and Crossflow Section Geometry
8.5.3 Bypass and Leakage Flow Area
8.6 Gasketed Plate Heat Exchangers
References
9 Heat Exchanger Design Procedures
9.1 Fluid Mean Temperatures
9.1.1 Heat Exchangers with
9.1.2 Counterflow and Crossflow Heat Exchangers
9.1.3 Multipass Heat Exchangers
9.2 Plate-Fin Heat Exchangers
9.2.1 Rating Problem
9.2.2 Sizing Problem
9.3 Tube-Fin Heat Exchangers
9.3.1 Surface Geometries
9.3.2 Heat Transfer Calculations
9.3.3 Pressure Drop Calculations
9.3.4 Core Mass Velocity Equation
9.4 Plate Heat Exchangers
9.4.1 Limiting Cases for the Design
9.4.2 Uniqueness of a PHE for Rating and Sizing
9.4.3 Rating a PHE
9.4.4 Sizing a PHE
9.5 Shell-and-Tube Heat Exchangers
9.5.1 Heat Transfer and Pressure Drop Calculations
9.5.2 Rating Procedure
9.5.3 Approximate Design Method
9.5.4 More Rigorous Thermal Design Method
9.6 Note on Heat Exchanger Optimization
References
10 Selection of Heat Exchangers and Their Components
10.1 Selection Criteria Based on Operating Parameters
10.1.1 Operating Pressures and Temperatures
10.1.2 Cost
10.1.3 Fouling and Cleanability
10.1.4 Fluid Leakage and Contamination
10.1.5 Fluids and Material Compatibility
10.1.6 Fluid Type
10.2 General Selection Guidelines for Major Exchanger Types
10.2.1 Shell-and-Tube Exchangers
10.2.2 Plate Heat Exchangers
10.2.3 Extended-Surface Exchangers
10.2.4 Regenerator Surfaces
10.3 Some Quantitative Considerations
10.3.1 Screening Methods
10.3.2 Performance Evaluation Criteria
10.3.3 Evaluation Criteria Based on the Second Law of Thermodynamics
10.3.4 Selection Criterion Based on Cost Evaluation
References
An electronic version of this book is available through VitalSource.
This book is viewable on PC, Mac, iPhone, iPad, iPod Touch, and most smartphones.
By purchasing, you will be able to view this book online, as well as download it, for the chosen number of days.
Digital License
You are licensing a digital product for a set duration. Durations are set forth in the product description, with "Lifetime" typically meaning five (5) years of online access and permanent download to a supported device. All licenses are non-transferable.
More details can be found here.
A downloadable version of this book is available through the eCampus Reader or compatible Adobe readers.
Applications are available on iOS, Android, PC, Mac, and Windows Mobile platforms.
Please view the compatibility matrix prior to purchase.